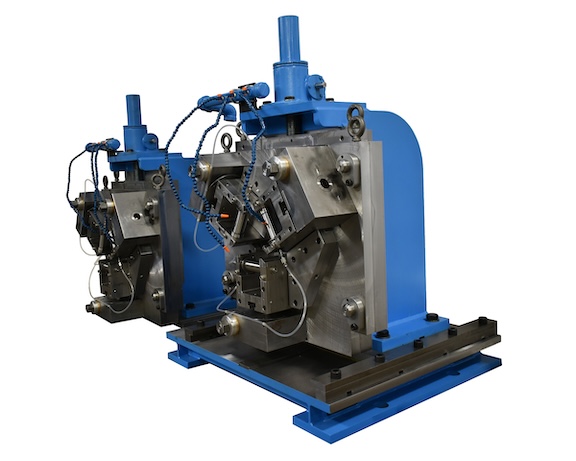
T&H Lemont recently shipped two identical heavy-duty three-roll weldboxes to a customer involved in manufacturing conduit and a variety of specialized tubing products. These weld boxes handle diameters from 2.500 to 5.00 in. OD and wall thicknesses from 0.050 to 0.188 in.
These custom-designed weldboxes, model WU-40, replace a pair of four-roll weld boxes designed and built by T&H Lemont. The customer had previously invested in smaller heavy-duty three-roll weldboxes for one of its mills and later expressed an interest in similar units with a few upgrades for a different mill.
The customer requested three design changes. First, the new units’ design provides improved visibility of the weld seam, allowing the operator to make process adjustments sooner. The second and third changes involved the customers’ existing roll-cooling process. The newly designed units include specially plumbed, water-cooled yokes for temperature control. The last upgrade is a coolant manifold with nozzles that direct the coolant toward the weld rolls. This flood system prevents weld spatter from sticking to the rolls and marking the product.
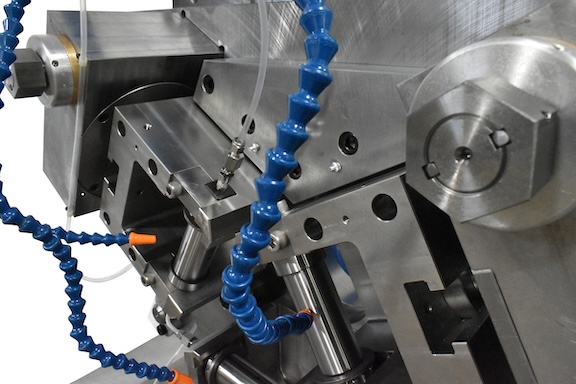
Designed for quick changes, the units have removable face plates so the operator can swap out the three clevises and tooling quickly. The operator loosens four set screws and swings the C washers out of the way, then uses the unit’s lifting hooks to remove the face plate. The next face plate is installed just as easily.
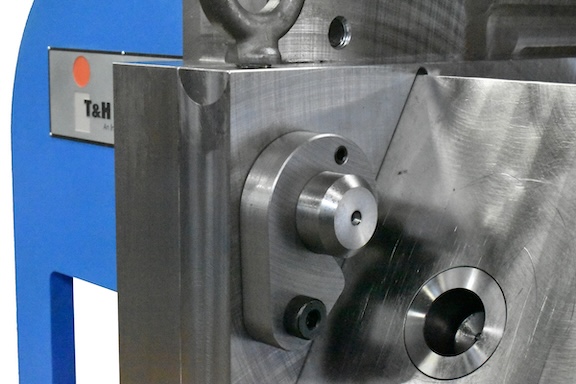
For ease of setup, the new units are gib-mounted and have three positioning adjustments—vertical, lateral, and upstream/downstream. Additionally, each roll clevis is equipped with a single-point adjustment that has a dial indicator to help the operator adjust the rolls precisely during every changeover.
The units likewise are designed for ease of maintenance, outfitted with zerk fittings at all the critical lubrication points. Furthermore, a convenient operator-side manifold simplifies the task of greasing the roll shafts, which require grease more frequently than the other points.